轧钢料剪切机的自动化控制系统设计与应用是一个综合性较强的课题,涉及到机械设计、自动化控制、计算机技术、传感器技术等多个领域。以下是该题目的一些研究内容和设计思路,供您参考:
1. 自动化控制系统的设计需求分析
生产效率要求:轧钢料剪切机的主要任务是切割轧钢料,控制系统需要保证在高效率、高精度下完成剪切操作。
剪切精度要求:由于轧钢料的形状和尺寸有严格要求,自动化控制系统需要实时调节剪切刀具与料的相对位置,确保剪切的精度。
安全性要求:自动化控制系统需要具备实时监控、故障报警、紧急停机等安全保护功能,避免因操作失误或设备故障造成安全事故。
设备状态监控:系统需要能够对设备的运行状态进行实时监控,及时检测到设备故障,保证生产的连续性。
2. 自动化控制系统的架构设计
PLC控制系统:使用PLC(可编程逻辑控制器)作为核心控制单元,能够实时处理剪切机的信号输入(如传感器、开关等)并输出控制指令(如电机控制、液压控制等)。
传感器与执行器:
位置传感器:用于实时监测轧钢料的位置,确保精确切割。
压力传感器:检测剪切过程中压力的变化,防止设备过载。
温度传感器:用于监控设备运行时的温度,避免因过热导致的设备损坏。
电动执行器与液压执行器:用于精确控制刀片的运动、压力和剪切力度。
HMI(人机界面):提供直观的操作界面,便于操作者监控设备状态、调整参数以及进行故障排查。
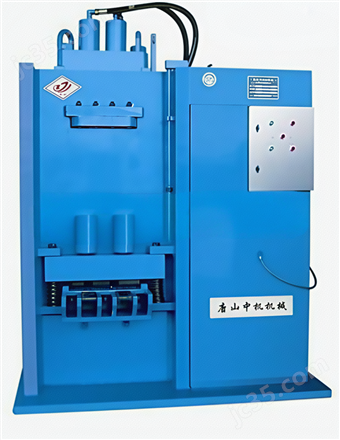
3. 控制系统的功能设计
自动剪切控制:根据输入的轧钢料的尺寸、类型和数量,自动计算剪切长度,调节刀片位置,并实现高精度的剪切。
速度与力量控制:自动调节剪切机的工作速度与剪切力量,确保剪切过程中不会对轧钢料造成过大压力或无法完成剪切。
自动检测与反馈:通过传感器实时监测剪切质量(如剪切面光洁度、尺寸公差等),将数据反馈给控制系统,自动调整设备参数。
故障诊断与报警:控制系统通过故障检测模块,能实时发现并报警,提示设备故障,避免损坏扩大。
4. 系统集成与通信
SCADA系统集成:通过SCADA(Supervisory Control and Data Acquisition,监控与数据采集系统)对整个生产线的各个设备进行集中管理与控制,实现数据的实时监控、远程控制和报警处理。
无线通信技术:利用无线通信(如Wi-Fi、蓝牙等)实现远程控制和监测,使操作人员能随时随地获取设备的运行状态和诊断信息。
数据存储与分析:通过数据采集与存储模块,记录每次剪切的参数、质量数据,并通过数据分析对生产过程进行优化。
5. 系统优化与提升
自适应控制算法:根据不同类型的轧钢料,自动调节剪切速度、刀片角度等参数,采用自适应控制算法,提高剪切的精度和效率。
节能设计:通过对电机、液压系统的精确控制,减少能源浪费,提高能效。
故障预测与预防:利用机器学习算法,分析设备的历史数据,预测可能出现的故障,并在问题发生前进行预警,避免停机损失。
6. 应用案例分析
案例1:某轧钢厂通过引入自动化剪切控制系统,成功提高了生产线的工作效率,减少了人工干预,提高了剪切精度,同时降低了设备故障率和维护成本。
案例2:在某钢铁生产厂,自动化控制系统集成了温度、压力、位移等多种传感器,通过对剪切过程的实时监控,实现了生产过程的全面数字化管理,并提高了生产线的自动化水平。
7. 挑战与未来发展
多样化轧钢料的适应性:随着不同种类、尺寸和材料的轧钢料不断变化,如何让控制系统能够灵活适应并保持高精度剪切是一个长期的挑战。
智能化与AI应用:未来,随着人工智能技术的发展,可以引入机器学习和深度学习算法,对设备运行状态进行智能优化和故障预测,提升系统的智能化水平。
总结
轧钢料剪切机的自动化控制系统不仅能够提升生产效率、提高剪切精度,还能通过智能化和数据化手段实现生产过程的优化和故障预测。随着自动化技术、传感器技术和人工智能的进步,未来的控制系统将更加智能、灵活,并在提高生产质量的同时降低能耗和设备维护成本。